Powerful Solutions for Electric Drives
Hairpins are bent parts made of insulated, enameled copper wire. They are used in the modern electric motors found in electric cars, hybrid vehicles, and e-bikes, where they replace the wound inductor coils that are part of conventional stators. Hairpin motors improve the power-to-weight ratio due to the packing density of the profile material.
WAFIOS offers state-of-the-art bending technology for producing hairpins, covering everything from small batches up to high volumes.
Machines
Machine comparison SpeedFormer
- Flexible change of hairpin geometries without retooling due to 3d bending technology that does not require any shape-dependent tools
- All hairpin geometries of a stator can be produced economically in batch size 1 by one machinery system
- The compatibility of machinery systems ensures a quick transfer of projects, if needed
- Reliable concept - from the development phase to series production - thanks to our WAFIOS production technology integrated in prototypes as well as large-volume series
- High output combined with minimum space requirements and low investment costs
- Quality control by integrated verification and control of geometry features, e.g. leg position or contact surface, using intelligent camera measuring technology
Please select Profilquerschnitt [mm²]
SpeedFormer
Transfer bending machinery system "SpeedFormer" for producing hairpins in series
With the SpeedFormer, WAFIOS offers a completely new approach to the cost-effective production of hairpins for the latest generation of electric motors. The SpeedFormer is the first machine that unites three proven bending techniques from conventional wire and tube bending machines in one unique system. One of the bending techniques has been used for decades in WAFIOS CNC spring and wire forming systems and has now been modified and optimized for the bending of hairpins. This technique is used for simple hairpin bends and ensures highest production speeds.
Reliable operation from prototyping to series production – Identical bending process on the prototype and series production line
The manufacturing principle of the FMU E prototype is transferred one-to-one to large-scale production. Therefore, there are no risks in the transition from prototype production to series production. The SpeedFormer reduces series production cycle times from 6-10 seconds per hairpin to 1-1.5 seconds per hairpin. Identical production technologies, i.e. the same tools and bending techniques, are used in series production.
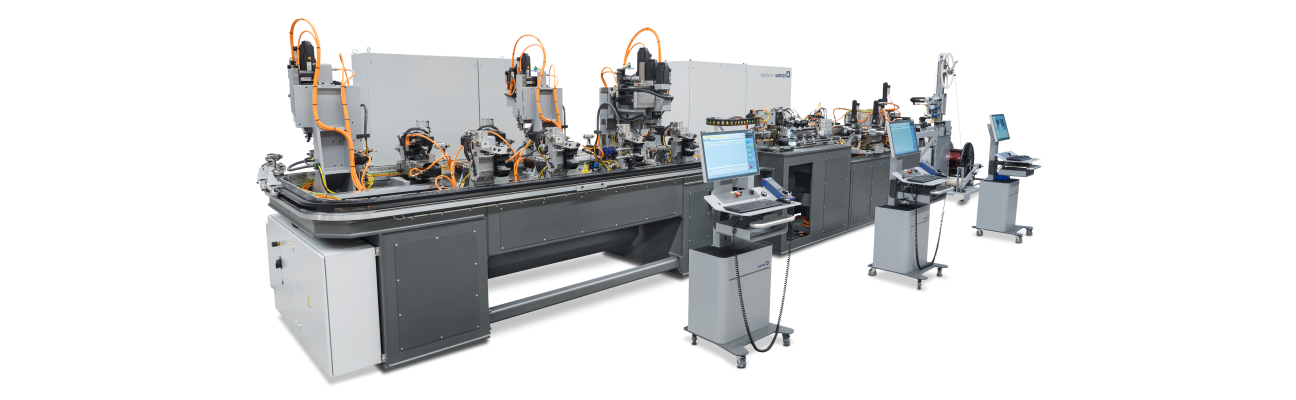