Enhanced Performance with Intelligent Software
iQ Functions from WAFIOS

iQ means using intelligent software solutions to get more performance out of your WAFIOS machine. The software add-ons help employees with set-up, increase the machine output or measure and improve quality automatically. For every type of machine, there are different iQ solutions available that are adapted to specific requirements.
Find out More about iQs !
Benefits at a Glance:
- No time-consuming re-programming due to generation of WPS program from existing spring
- Alternative systems transferred to the WAFIOS Programming System
- Faster set-up due to automatic generation of the WPS program
- Operator assistance through simplified set-up process
- Small adjustments are made subsequently by hand or using iQautopitch
Areas:
iQspring+ – Automation of the set-up process to prevent collisions and to increase the output
Benefits at a Glance:
- Early detection and automatic prevention of collisions before the bending process
- Increase in output due to optimization of the axis traversing paths
- Determination of cycle times for accurate production planning
- Reduced downtime due to digital testing of the machine
- Simplified optimization of programs
- Visual training for in-house employees
- Fewer rejects during the set-up of the machine
- Feasibility simulation before the bending process
Areas:
iQcontrol – In-process control of spring length, end position, and diameter
Benefits at a Glance:
- Considerable minimization of rejects through in-process control of each individual spring
- Enhanced machine capability due to reduced variation of spring length and end position
- Enhanced process reliability due to self-learning control
Areas:
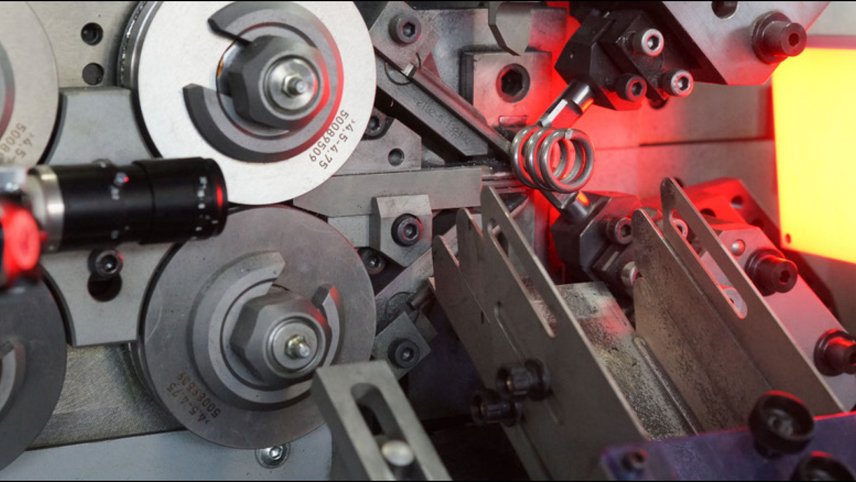
iQsmartbend – Quality and performance enhancement through automatic optimization of bent parts
Benefits at a Glance:
- Increased output with consistent quality through active reduction of vibrations
- Increased machine availability due to shorter set-up times
- Fewer rejects during set-up
- Faster set-up thanks to automatic calculation of ideal NC parameters
- Operator assistance through simplified set-up process
Areas:
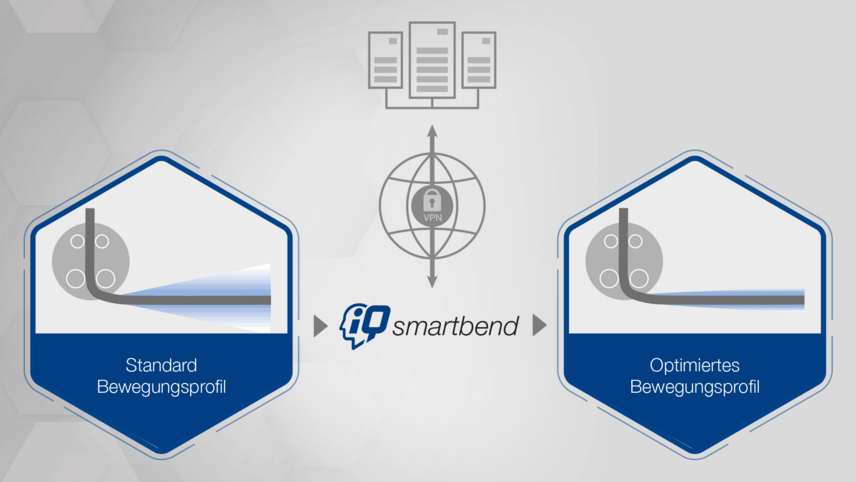
iQ Solutions by Type of Machine
Copying a compression spring by means of an external measuring device | iQspring2FUL |
Camera measuring system with flying rotating cut | iQopticut |
In-process control of spring length, end position, and diameter | iQcontrol |
Calculation of the optimal feed speed | iQbestspeed |
Automatic pitch and diameter correction with an external measuring device | iQautopitch |
Enhanced quality through angular dressing of grinding wheels | iQalphadress |
Quality enhancement through synchronization of the loading and grinding time | iQbestload |
More efficient grinding of spring ends due to simple analysis and optimization of the spring end grinding process | iQsmartgrind |
Improving the quality and performance of the spring end grinding process by means of a temperature-controlled grinding technique | iQtemperature |
Reduction of set-up work due to simple adjustment of variable dressing speeds | iQvariodress |
Reduction of set-up work due to simple adjustment of the production sequences of one- or multi-layered wave springs | iQwavespring |
Reduction of set-up work due to simple adjustment of bending speeds | iQbend |
In-process measurement and control of the bending angle | iQbendcontrol |
Automatic conversion of CAD data to WPS geometry programs | iQconvert |
Automatic correction of components by means of an external measuring device | iQinspect |
Quality and performance enhancement through automatic optimization of bent parts | iQsmartbend |
Workpiece and tool breakage control through monitoring of the motor torque | iQtorque |
Simulation of the bending process with collision monitoring and determination of cycle time | iQwire |
Automation of the set-up process to prevent collisions and to optimize the position of the table | iQwire+ |
Reduction of set-up work due to simple adjustment of bending speeds | iQbend |
Automatic conversion of CAD data to WPS geometry programs | iQconvert |
Optimization of set-up times through simplified programming of free-form geometries | iQfreeform |
Automatic correction of components by means of an external measuring device | iQinspect |
Quality and performance enhancement through automatic optimization of bent parts | iQsmartbend |
Workpiece and tool breakage control through monitoring of the motor torque | iQtorque |
Automatic positioning of tubes with punched-in holes and markings before the bending process | iQtubeorientation |
Simulation of the bending process with collision monitoring and determination of cycle time | iQtube |
Automation of the set-up process to prevent collisions and to optimize the position of the table | iQtube+ |
In-process straightness measurement of straightened rods | iQm-straight |